Optimize inventory, enhance service,
and increase margins
Who says you can’t have it all? We help clients identify and implement cost-saving improvements across their value chain, leveraging our expertise in operations, engineering, and finance as well as 25+ years of experience with Class I, II, and III medical device manufacturers. We also provide small-scale, clean room manufacturing and assembly at our new facility in Corona, California.
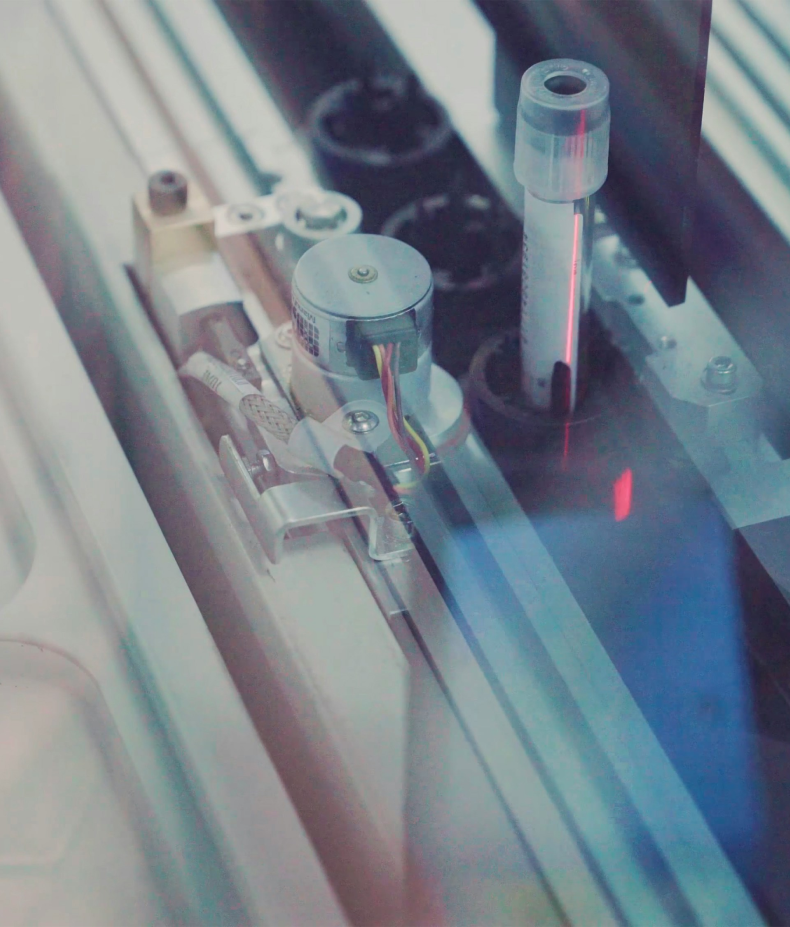
Whether you’re a small startup or a global manufacturer, we can meet you where you’re at. Here are just a few of the ways we help companies optimize inventory and unlock profit.
1/4
Innovation and
creation
creation
- Feedback for design/manufacturability
- Small volume manufacturing in our Corona facility: ~ 200 FT hard wall clean room (ISO Class 8); manual manufacturing assembly area with ESD controls; documentation infrastructure
- Manufacturing/commercialization plans
- Review of supplier/quality contract agreements
- Accurate product costing (including overhead, labor, and material)
- Specifications and requirements for manufacturing or design transfer
Interface with contract manufacturer to translate information and qualification requirements into practical actions and solutions
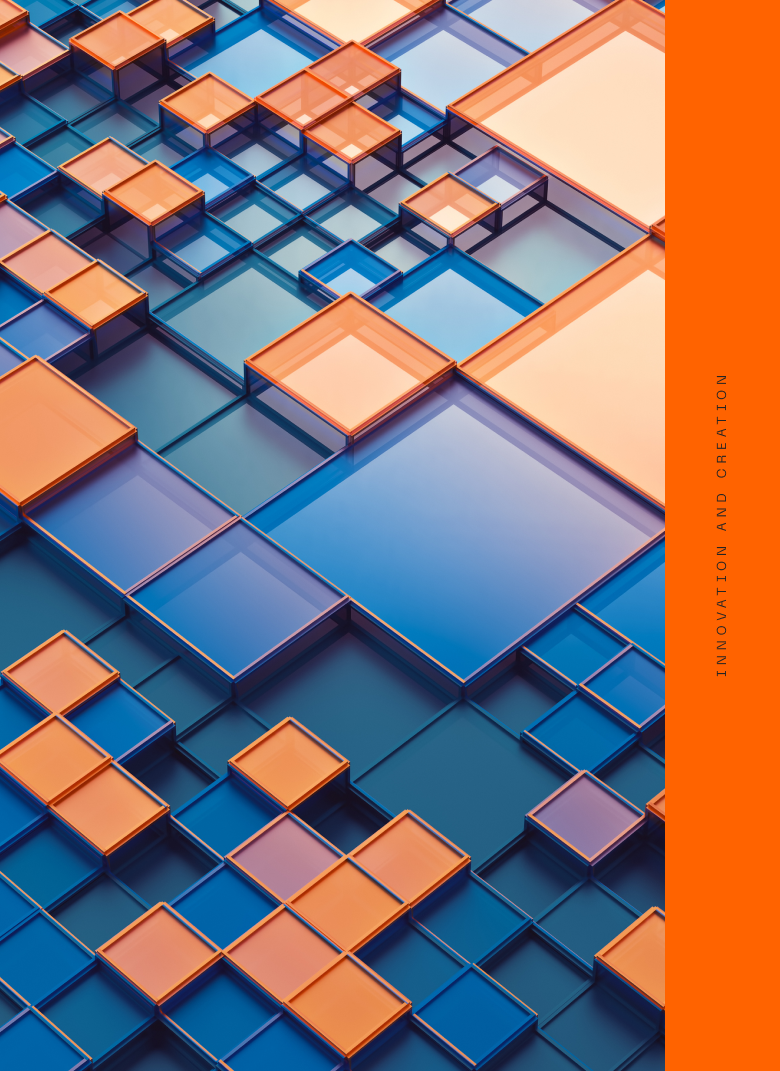
2/4
Manufacturing transfer
- Design and development planning (quality plan, facility validation, master validation plan)
- Equipment, software, and process validation expertise
- Manufacturing documentation infrastructure
- Cost simulation / modeling
- Operation planning and execution
- Packaging validation support/testing
- Technical documentation / risk management implementation
- Contract manufacturer (CMO) interface
- Supply chain / demand response setup
- Establish supply-to-demand tool
- Establish and organize master data
- Integrate tools with customer service
3/4
Large scale
manufacturing
manufacturing
- Direct support to operations, manufacturing, engineering, and quality roles
- Production ramp planning and execution
- Processes to reduce inventory and improve service level for growing companies
standardized tools for due diligence assessments evaluating QMS maturity, commercialization capabilities, and operational and product cost performance
- Flexible manufacturing and operations planning and execution tools for companies that have not transitioned to large ERP systems, e.g., SAP, Sage, Oracle, JD Edwards, etc.
- Capacity improvements
- Project management
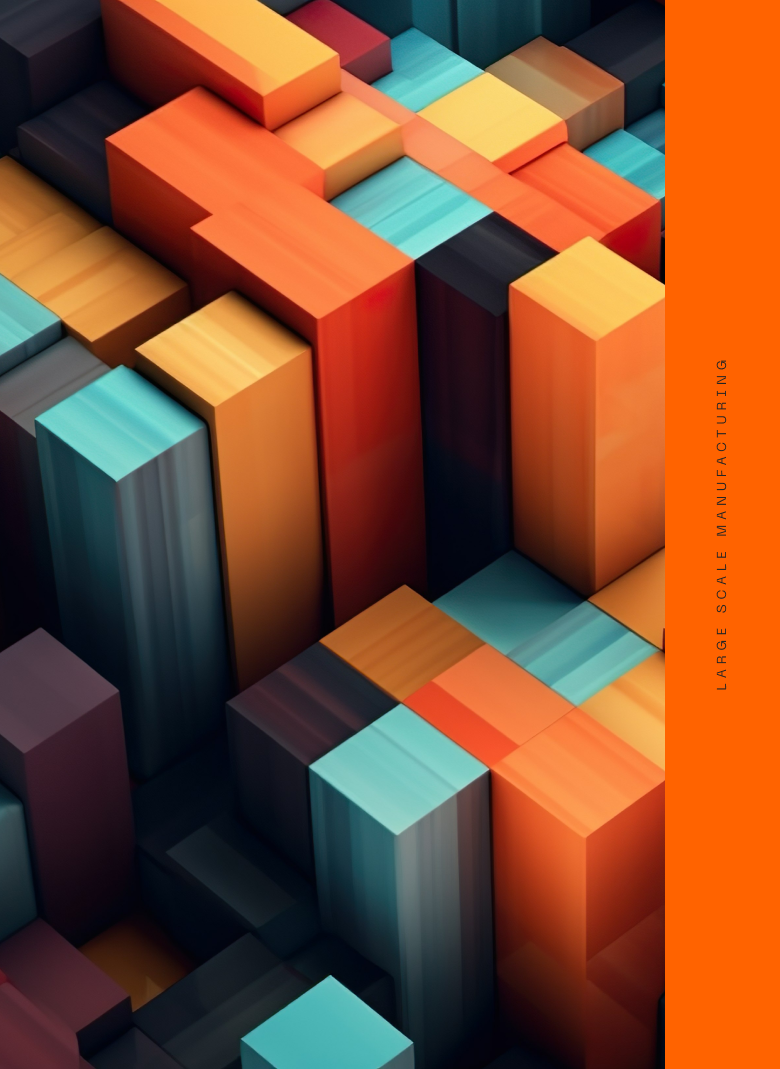
4/4
Quality, compliance, and remediation
- EU MDR remediation of QMS and technical documentation for Class II and Class III products
- Procedure updates and direct audit support for both transitional and
- QMS updates required by MDR through stage 1 audit and site approval of multiple QMSl
- Technical guidance and process for technical documentation remediation
- Risk management upgrades and processes to maintain compliance
- Electronic IFU services
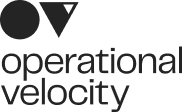
Operational Velocity
109 N Maple St, Unit J
Corona, CA 92878-3298
951 475 7038 | 949 445 0532
contact@operationalvelocity.com
© 2024 Operational Velocity